Barcode Warehousing
Anyone who has worked in a facility where inventory is tracked manually understands the hassle that simple day-to-day operations can be. These include actions such as locating, moving, and consuming inventory. Keeping track of these simple actions on paper is time-consuming, inefficient, and leaves your operation vulnerable to human error. For example, such an error could bring your entire production to a stand-still because someone forgot to mark on the paperwork that a raw material is no longer available for consumption.
CMS puts these problems to rest. At the heart of CMS is its ability to track inventory at the container level. Customers who utilize container-level tracking typically see inventory accuracies in excess of 99.9%. This is all possible due the system’s ability to assign each piece of inventory a unique bar-coded label. This label acts as a “license plate” which the system uses to keep track of and update the inventory automatically and in real-time. With this system, keeping track of your operations is as easy as scanning bar-codes.
Container Level Inventory
Gone are the days of item / lot tracking. With Valdata, all containers are individually license plated. This, in combination with direct scale connectivity, gives 99.9% accurate inventory.
Instead of annual (or worse yet quarterly) physicals, with CMS, companies continuously correct quantities every time a container is emptied.
Click the video to see how!
Easily Move Inventory
Older warehousing systems often require the manual recording of at least 5 pieces of information to move a container. They are usually: item, lot, from-location, to-location and quantity. Manually recording all of this information is both time consuming and leaves you vulnerable to human error.
CMS was designed to make moving inventory as simple and accurate as possible. Simply scan the container or pallet being moved, then scan the location it is going to. With just two bar-code scans, CMS automatically updates your warehousing data with all of the information above, and more.
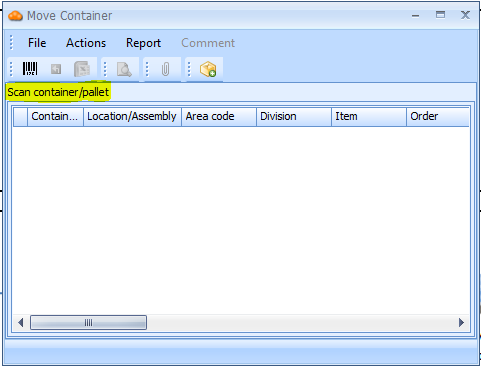
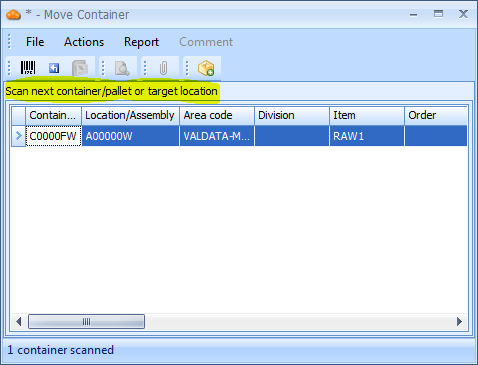
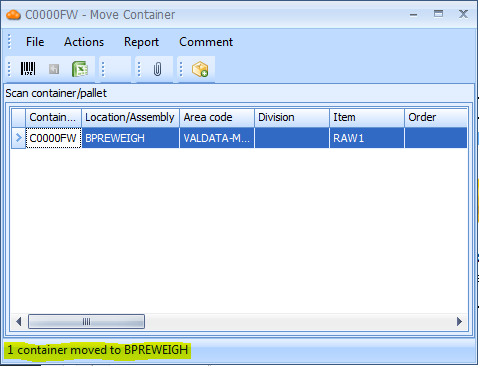
Verify Location
It is important to periodically make sure that everything in your inventory is where it should be. This is done by a process called location verification. Traditionally, this involves going to a location with a piece of paper and comparing every item in that location to where your warehousing system says it should be. Items that aren’t where they should be would then have to be either moved or manually updated in the system.
Once again, this is another time-consuming process that CMS makes quick and easy. Simply scan the location, then scan all of the items in that location. This allows the software to verify that all items are where they should be.
Items that are scanned, but marked as being somewhere else are then updated to their scanned location; and items that were not scanned that should have been there are then marked in the system as being “missing” until they are located elsewhere.
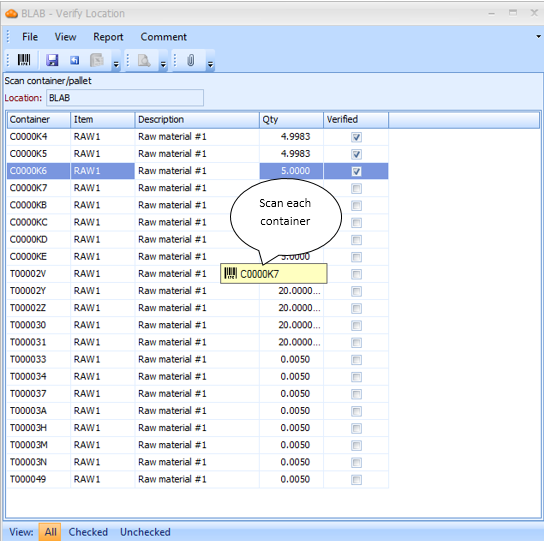
Forward or Reverse Tracing
Forward and reverse tracing are processes by which you can track where materials were used and where they came from. This functionality is especially important for when something goes wrong in manufacturing. Traditionally, you would have to go through all of the orders and inventory logs by hand to figure out where a material was used and where it came from.
Thanks to CMS’s barcoded warehousing system, you are able to trace every step forwards or backwards from raw ingredients to finished products.
Staging
Staging is a process by which you make sure enough materials are in the right areas to fulfill current or impending orders. For example, if you have 10 kg of a raw material available in your batching area, but your orders call for a combined amount of 100 kg of that material, you would need to get another 90 kg to the batching area immediately.
Staging can be a real hassle if done manually. It involves looking through your orders and going ingredient-by-ingredient to see which materials need to be brought over. CMS makes this process incredibly easy. In the staging window, the demand from every location for each material is displayed. It also displays the specific containers of each material and their locations. With this information, a worker can then simply scan each container to be staged. CMS then automatically updates warehousing information in the system.
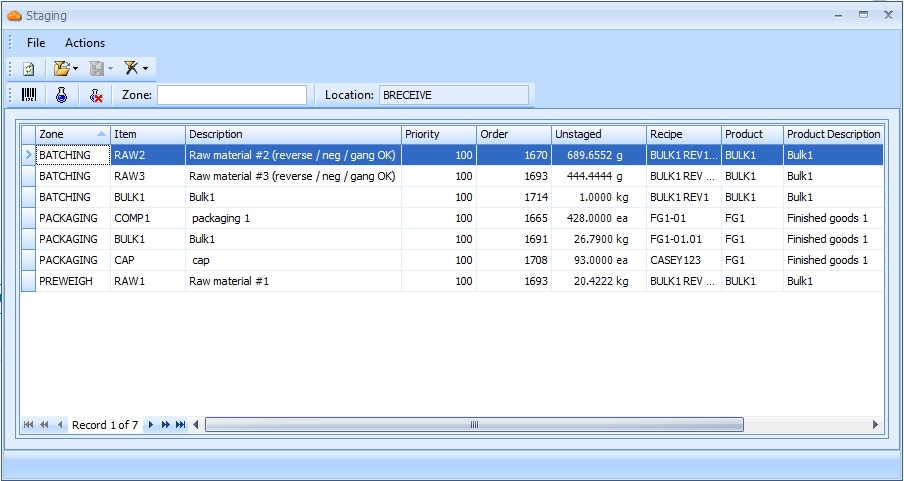
Create Pallet / Assemblies
CMS has a lot of flexibility in how it can manage inventory. For example, individual items such as drums and bags can be grouped together into pallets or assemblies. This function allows you to move large numbers of individual containers together until they need to be handled individually.
Transfer Cans
In many facilities, small containers are used to transfer weighed amounts of material from a larger source container. These small containers are then used to transfer and add raw ingredients to batching orders. Through the use of bar-coded labels, CMS has the ability to manage these “transfer cans”, prompting the dispensing to and addition of materials to and from transfer cans.
Automatically Adjust Inventory
With CMS, you no longer have to worry about manually adjusting your inventory every time you dispense or transfer material from one container to another. After dispensing, CMS automatically updates the inventory for both source and target containers, including when the source container is marked empty.
Shipping Errors
Putting together and shipping out the wrong finished goods is not only a huge time and money waster, it can also cause your customers to lose confidence in you as a consistent and reliable supplier. CMS helps to eliminate shipping errors with the use of bar-codes. Even while assembling an order to be shipped out, CMS allows for items to be scanned to ensure that the order is correct.
Reweigh / Re-measure
CMS has the ability to weight the contents of a container without having to transfer the material for taring. This is possible because containers can be assigned tare weights right in the system. Tare weights can also be entered manually while weighing if the container’s tare weight is not in the system.
Reweigh Prompts
Reweighing is important for making sure your containers really have the amount of materials you think they have. This is especially important as you approach the end of a container.
CMS has the ability to automatically prompt to reweigh a container when it believes the remaining quantity is less than a certain percent of the original container size. This simple feature can save you from the many headaches caused by not having the amount of material you think you do before committing it to an order.
Random Put-Away
Many software packages enforce that containers be put in specific locations based on various organization systems. These might be based on alphabetical order, container size, and material type. Although this might sound like a good way to organize inventory, this sort of inflexible system often causes more problems than it solves. For example, containers that are handled often tend to naturally get placed in a location that allows for easy access. CMS does not enforce any sort of put-away system and therefore allows for containers to be put wherever they work best.